Tipping drums is an essential part of many industrial processes. Our drum rotators provide a safe way to lift and tip various drum types and sizes, and we can customise each rotator to suit your exact needs.
Bespoke ATEX Pharmaceutical Drum Handling Machine
Bespoke drum handling for pharmaceutical production, ensuring safety, hygiene, and operational efficiency.
When a leading pharmaceutical manufacturer needed a bespoke drum handling solution for their facility, they turned to STS. The project came with a unique set of challenges, requiring equipment that could handle a wide range of drum sizes and materials while meeting strict hygiene and safety standards in an environment where flammable powders are present.
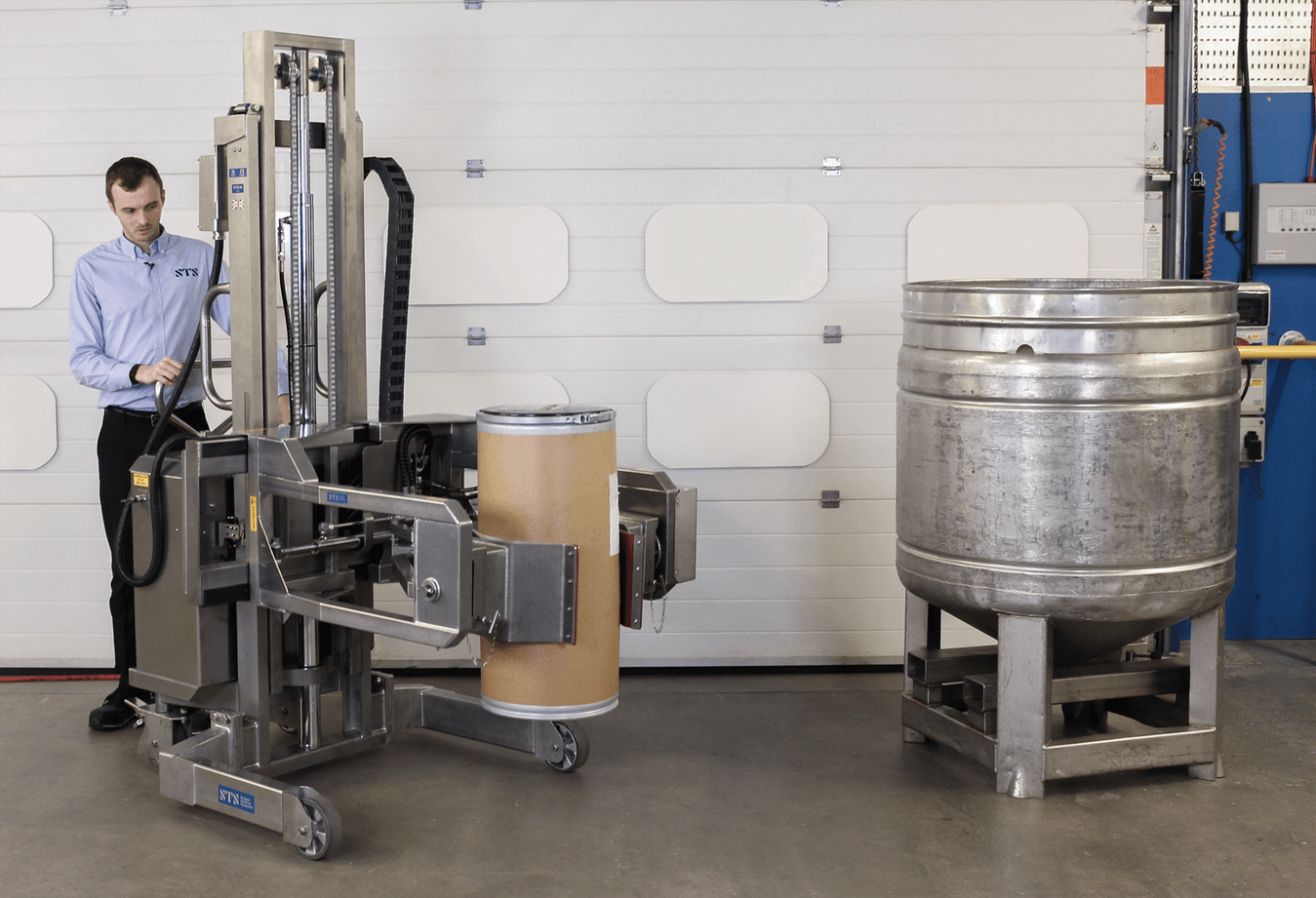
Project Requirements
The customer's requirements were clear but complex:
- Hygiene and Safety Compliance: The equipment had to be manufactured from 304-grade stainless steel to meet rigorous hygiene standards, ensuring a clean working environment in their facility.
- Versatile Drum Handling: The machines needed to handle a broad range of drum sizes, from 50 to 220 litres (13 to 58 gallons), made from various materials, including steel, plastic, and fibreboard. These different materials each present unique challenges, requiring flexible clamping solutions to prevent damage or deformation.
- Height and Tipping Flexibility: The project included two machines – one with a standard tipping height of 1500mm (59 inches) and another with a telescopic dual-mast design for tipping drums at heights up to 2500mm (98 inches), providing flexibility for various production processes.
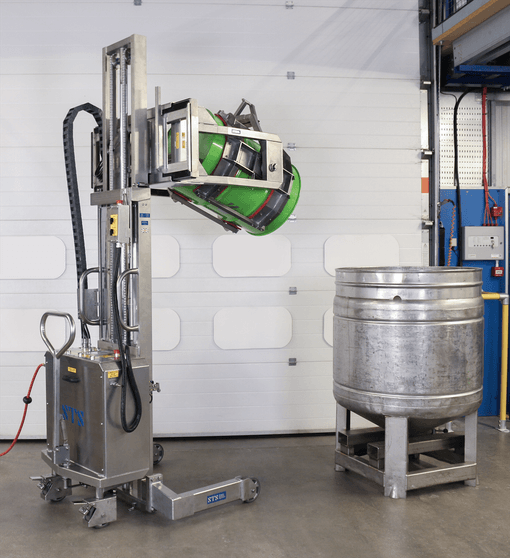
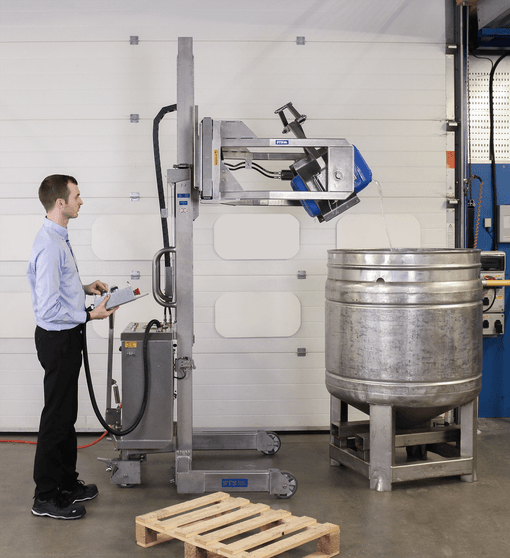
Custom Engineering and Modifications
To meet these needs, STS developed two bespoke drum handling machines with several innovative modifications:
- Interchangeable Clamping Pads: To accommodate the wide range of drum sizes and materials, two pad types were developed. Larger pads were designed for secure handling of 205-litre (55-gallon) drums, while smaller pads were tailored for lighter, more delicate drums ranging from 50 to 120 litres (13 to 32 gallons). These pads can be quickly swapped by operators depending on the drum type, size, and weight, making the machines highly versatile.
- Clamp Pressure Control: To prevent crushing or damage to softer drums, each machine was fitted with a large, easy-to-read clamp pressure gauge, allowing operators to apply just the right amount of pressure.
- Pendant Controller for Enhanced Operator Control: To improve safety and precision during high-level pouring operations, a pendant controller was installed. This allows operators to stand at a safe distance alongside the machine with a clear view of the tipping process, reducing the risk of spillage and ensuring valuable materials are handled with care.
Results and Customer Benefits
- Enhanced safety in flammable ATEX environments
- Flexible, efficient handling of various drum sizes and materials
- Reduced risk of drum deformation or damage
- Improved operator visibility and control during the tipping process, reducing the risk of costly spills

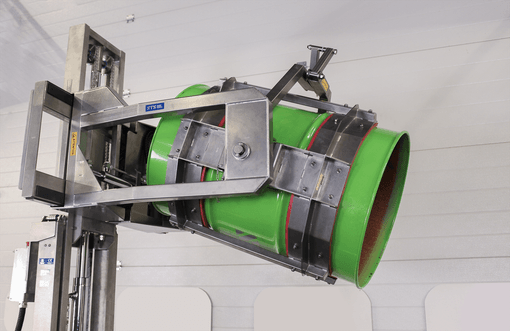
Conclusion
This project highlights STS's ability to deliver tailored drum handling solutions for demanding pharmaceutical environments, demonstrating our commitment to safety, precision, and customer-focused engineering.
Drum Rotators / Tippers
Contact Us
If you need a custom manual handling solution, we can design and manufacture the right piece of equipment to meet your specific requirements. Talk to us to find out how we can help you.